振れ止め機能付き天井クレーン
現在、天井クレーンは国内外問わず様々な工場で重量物を運ぶために多用されています。しかし、天井クレーンは荷を運ぶ際に荷振れが生じ、この振れが大きければ周辺のものとの接触や荷崩れなどの危険を及ぼす可能性もあります。
熟練の運転者であれば荷の振れを抑える技術を習得していますが、経験の浅い運転者は振れを抑えることに時間を要し、特に加速時および減速・停止時は振れを止めようと、つり荷に意識が集中し、周囲への注意が散漫になる傾向があります。
そこで、荷振れの小さい天井クレーンの普及が必要と考え、振れ角などを検出する特別なセンサを用いず、最小限の追加費用で運転者を支援する つり荷の振れを抑制する振れ止め機能付き天井クレーンを開発しました。
振れ止め機能付き天井クレーンのシステム構成を図1に示します。この構成は当社の従来のインバータ制御天井クレーンと同じです。
操作器やリミットスイッチ・センサからの信号をPLC(Programmable Logic Controller)に入力し、予め記憶させたプログラムに従いインバータや補助リレー・電磁接触器等の装置に信号を出力してモータ・ブレーキを動作させ天井クレーンを制御します。
従来、天井クレーンのつり荷の振れを抑制するためには、振れ角、ワイヤの長さ、移動速度などをセンサで計測 し、その計測値を基に制御する方法が一般的でした。しかし、センサの設置費用やメンテナス費用がかかる、また、センサが故障した場合に信頼性が失われるなどの課題がありました。
こうした課題に対応するため、つり荷の振れ周期、トロリの横行速度、クレーンの走行速度などの特性をもとに作成したシミュレーョンモデルにより、つり荷の振れを予測しリアルタイムに反映して適切に速度制御することで、振れ角センサなどを用いないシステム構成で振れ止めを実現しました。
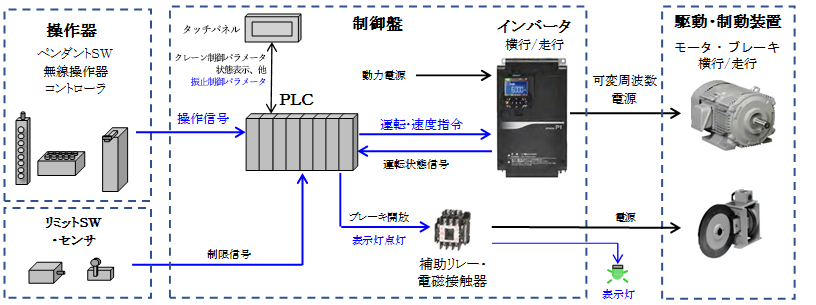
図1 インバータ制御天井クレーンの電気制御機器構成
振れ止め機能付き天井クレーンの制御ブロック図を図2に示します。
従来のクレーン制御プログラムから出力された速度指令値を振れ止め制御プログラムで処理し、振れを抑制する速度パターンの速度指令値をインバータに出力します。
この速度指令に対して、つり荷がどのように振れるかを常にリアルタイムでシミュレーションして、速度指令値を補正します。リアルタイムで常時シミュレーションするため、加速の途中で釦を放し減速したり、減速の途中で釦を押して加速しても、又、同時に巻上または巻下しても振れを抑制できます。
振れ止め制御にはクレーンの速度及び加速度、振り子長が必要です。クレーンの速度及び加速度はクレーンの仕様により決まります。
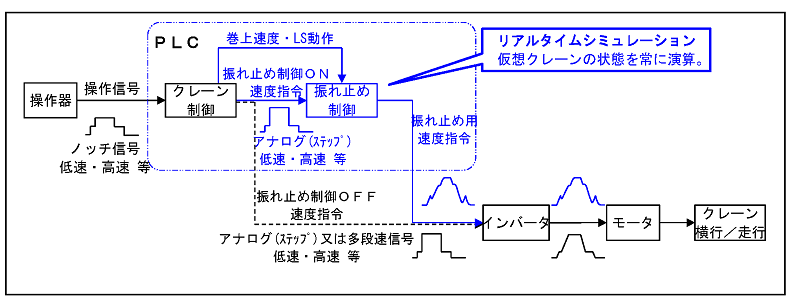
図2 天井クレーンの振れ止め制御ブロック図
振子長については、単振り子の場合は支点からおもりの重心までの距離ですが、クレーンの場合は支点がドラム、イコライザシーブやヘッドシーブと複数あるのでその平均位置を仮想の支点とし、つり荷の重心までの距離が振子長になります。
具体的には図3のとおり、仮想の支点からフック重心までの距離 LF とフック重心からつり荷の重心までの距離 LW の和が振子長 L となります。
実機では仮想の支点からフック重心までの距離は巻上の速度と運転時間やインバータの速度(周波数)モニタ値などから計算して求めます。しかし、フック重心からつり荷重心までの距離は簡単に検出や計算が出来ないので運転者にて設定する方式としました。
例えば、予め3段階の距離を記憶させ釦を押すと1番目の距離、もう一度押すと2番目、もう一度押すと3番目、もう一度押すとつり荷無しにしたり、いつも同じ高さで横走行するのであれば、固定値に設定するなど、お客様の使い方に合わせた方法で納入しています。
尚、振子長は振れ止め制御に重要ですが、10%程度の誤差があっても目標の振れ幅に入り、20%の誤差があったとしても、振れ幅は大きくはなりますが、振れ止めの効果は十分あります。
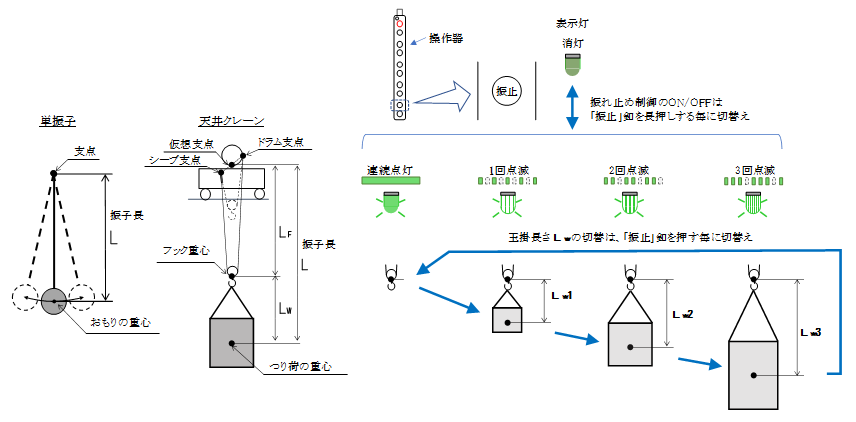
図3 天井クレーンの振り子長 および フック重心からつり荷重心までの距離設定方法例
図4は振れ止め制御OFFで10秒間操作釦を押した場合のクレーンとつり荷の速度、及び振れ幅を示したものです。加速中はつり荷が遅れて後に振れ、減速中につり荷が前に振れて、クレーンが停止した時には大きく振れています。(定格速度0.667m/s、加減速時間4.0s、振り子長9.0mで振れ幅±0.46m程度。)
それに対し、図5は振れ止め制御ONで同じく10秒間操作釦を押した場合のクレーンとつり荷の速度、及び振れ幅を示したものです。加速を開始してすぐに一旦加速を緩めて再加速し、つり荷の振れをクレーンの加速度に応じた傾きに保ち、加速が終わる直前に一旦減速し再加速して最高速度になった時点でつり荷の振れを小さくしています。減速時は加速時と同様に減速を開始してすぐに一旦減速を緩めて再減速し、つり荷の振れをクレーンの減速度に応じた傾きに保ち、停止直前に一旦加速して再減速し停止した時点でつり荷の振れを小さくしています。
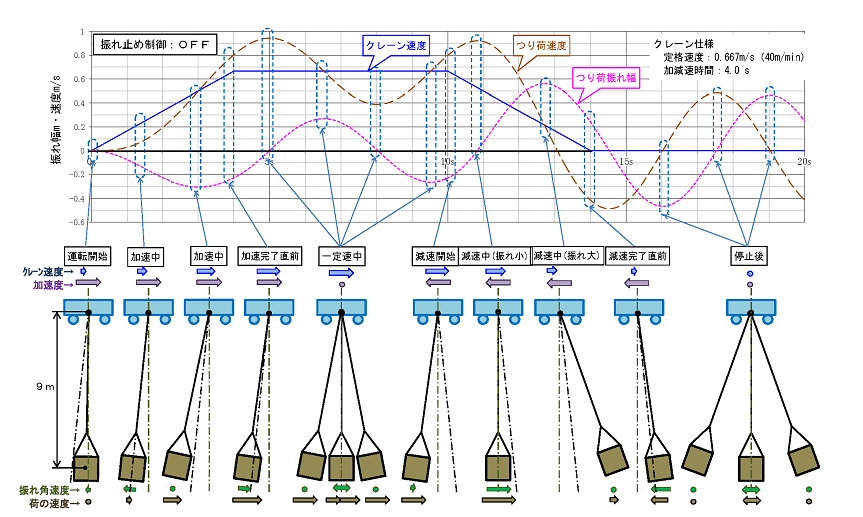
図4 振れ止め制御OFF時のクレーン速度とつり荷の速度及び振れ幅
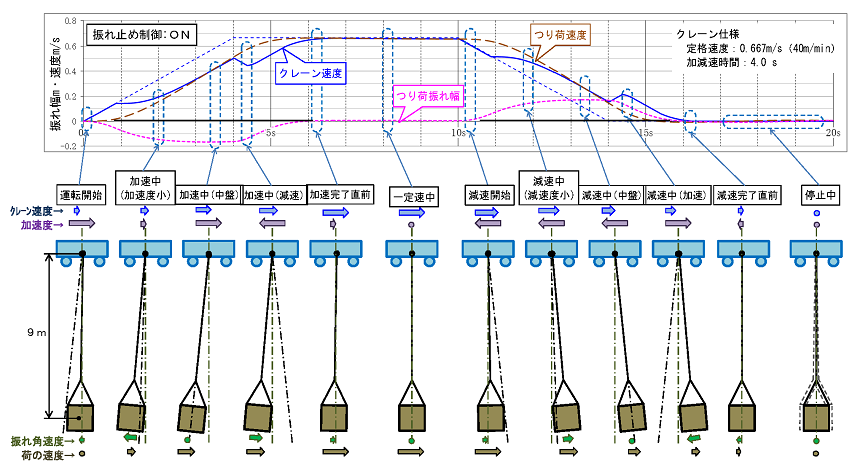
図5 振れ止め制御ON時のクレーン速度とつり荷の速度及び振れ幅
1回の運転で発生する最大の振れは、振れ周期の半分の時間で加速し、減速した場合になります。
図6に示す通り、その振れ幅は加減速時の加速度による振れ中心の傾き角θの4倍に達します。
速度0.667m/s、加減速時間4.0s、加速度0.167m/s2の場合、およそ±4°の振れ角になり、振子長 9.0mであれば、約±0.6mの振れ幅となります。
この振れ幅の10%、最小値±50mmを目標値としました。各振子長ごとの目標値を表1に示します。
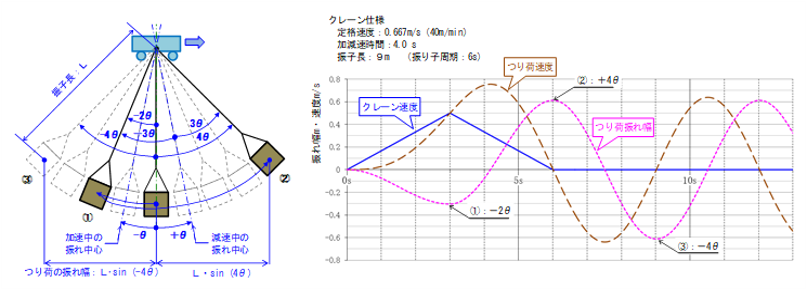
図6 1回の加減速動作で最大となるつり荷の振れ幅
表1 振れ止め制御時の振れ幅目標値(加速度0.167m/s
2の場合)
一例ですが、実際にお客様に納入した天井クレーンにて、運転中のインバータへの速度指令値とつり荷の振れ幅をレコーダで記録し、停止後のつり荷の振れ幅は目視による実測も行いました。結果は図7と表2の通りです。
定格速度0.5m/sまで4.0sの加速度で起動し、約13.2s運転後に約4sで減速し20mm/s(4%)の微速で目的位置の10mm手前まで運転し、停止させています。
振り子長5.6mで最大振れ幅±27mmとなり目標値の±50mm以内でした。
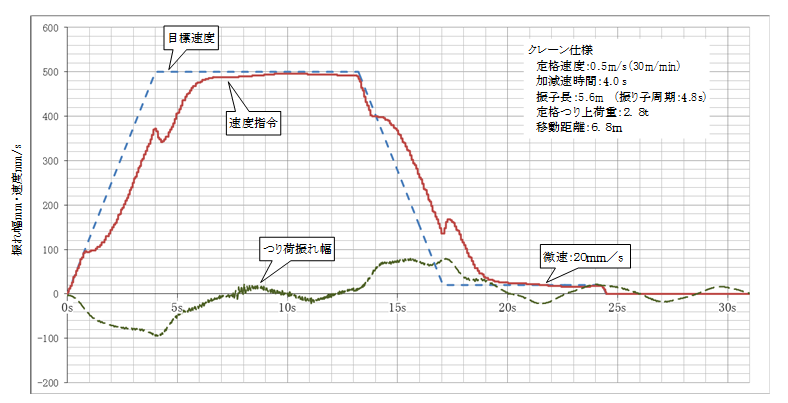
図7 実機のつり荷の振れ幅レコーダ記録(測定結果1回目)
表2 実機の振れ幅目視測定値
又、お客様にご協力頂きペンダントスイッチ操作式の天井クレーンをお客様のベテラン運転者と弊社の初心者6名にて操作を行い、図8の搬送ルートの両方向で振れ止め制御OFFとONの搬送時間及び操作回数の比較を行いました。結果は表3の通りです。
振れ止め操作に不慣れな初心者では搬送時間、操作回数共に大きな効果がありました。ベテランの場合は搬送時間に効果は無いが、操作回数は約40%低減しています。
シビアな位置合わせが必要な製造設備の置台への搬送より、ラフな型置場への搬送の方が効果が大きいことが判りました。
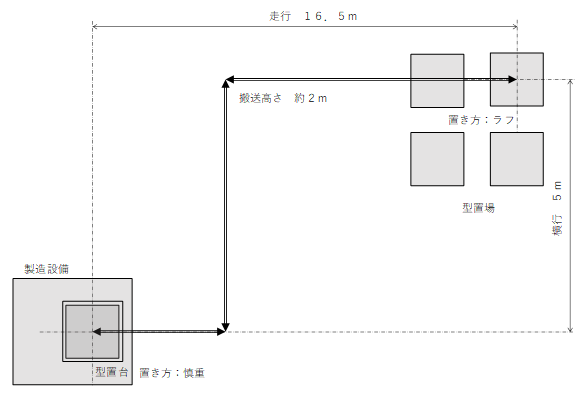
図8 搬送時間及び操作回数測定時の搬送ルート
表3 実機での搬送時間及び操作回数
2017年より当社工場の天井クレーンに本振れ止め制御を搭載し実際にお客様に見学及び体験して頂き、好評を得ています。
振れ止め制御時は減速停止距離が延びる傾向ですが、減速開始を早めにすれば位置合わせにも問題なく、特に巻上・巻下と同時操作しても、又、横行走行同時操作しても荷が振れないことで評価を頂いています。